Projects
Sellafield – Main & North Security Gate Installation
One of our more recent projects based within Sellafield Ltd was to install the new security gates to the Main inbound entrance as well as the North In & Out bound entrances to the nuclear site.
As a company, LEL Nuclear has been heavily involved from the start of this project right through to the commissioning stage of each gate. LEL Nuclear was tasked to create all the required documentation including Risk assessments, ICL’s, Quality plans and so much more required for a smooth install. Following the acceptance of all documentation, LEL Nuclear worked tirelessly through many night shifts to install the gates whilst minimising disruption to the site and local highways.
All 3 gates are now fully installed, commissioned and handed back over to Sellafield Ltd.
Shaun Sweeney (Senior Works Manager) working on behalf of the main contractor ‘Morgan Sindall’ had went on to say that: “Nick and his LEL Nuclear team are a breath of fresh air to the Sellafield Site, they are highly skilled and their attention to detail is ten to none”.
Sellafield - BEPPS DIF - Shield Door Refurbishment
Located at the Sellafield Ltd site, this marked the first significant project undertaken by LEL Nuclear. Commencing in 2018, our initial assignment involved refurbishing the main shield door for the BEPPS DIF project. This encompassed a multitude of intricate installations, such as seismic restraints, door drives, air skates, pneumatic control boxes, recovery systems, pipework, and various other elements.
As a result of our exceptional performance and commitment to outstanding workmanship, numerous opportunities emerged within the project. These opportunities included involvement in numerous additional complex installations, rigging tasks, and collaboration with the SL commissioning team. Our responsibilities extended to performing all remaining mechanical snagging work on the project, showcasing our capabilities and dedication to excellence.
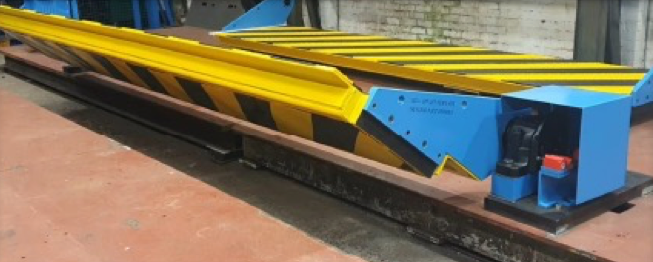
BAE Systems - Shield Door Shielding Installation
After proving ourselves with the shield door installation work within Sellafield, we then managed to win the contract for the shielding installations within the new dreadnaught submarine workshops based at BAE systems in barrow.
The job initially consisted of drilling and tapping countless holes to allow for the installation of shielding plates before using a specialist putty to place between the plates to ensure no radioactive rays are able to escape the area.
Holmen Iggesund – Valve Overhaul
Upon the successful completion of various projects across several different high profile sites, LEL Nuclear have expanded out into providing services to local business through our extensive list of capabilities.
LEL Nuclear have recently undertaken several projects within the Holmen Iggesund premises from steam trap surveys, condition reports to a complete valve overhaul. The valve overhaul consists of a large seized double disc gate valve which had to be jacked out with over 3 tonnes of force. Upon removal the faces were found to be damaged and therefore resulted in the requirement for lapping of the internal valve seats as well as machining both disc faces. Now with perfect sealing faces on both components, the valve was reinstalled and the discs packed accordingly to ensure a good seal was provided between the two faces.
Following re-installation, further opportunities have arisen throughout the Holmen Iggesund site where LEL Nuclear look forward to supporting them through many more complex projects.
Flask Lid Turning Machine
This project was based within Sellafield Ltd where we were tasked with installing the new security gates to the Main inbound entrance as well as the North In & Out bound entrances to the nuclear site.
As a company, LEL Nuclear has been heavily involved from the start of this project right through to the end of the commissioning stage of each gate. LEL Nuclear was tasked to create all the required documentation including, but not limited to: Risk assessments, ICL’s, Quality plans, COSHH assessments, Method statements and more, required for a smooth install. Following the acceptance of all documentation, LEL Nuclear worked tirelessly through many night shifts to install the gates whilst minimising disruption to the site and local highways.
All 3 gates are now fully installed, commissioned and handed back over to Sellafield Ltd.
Shaun Sweeney (Senior Works Manager) working on behalf of the main contractor ‘Morgan Sindall’ went on to say that: “Nick and his LEL Nuclear team are a breath of fresh air to the Sellafield Site, they are highly skilled and their attention to detail is ten to none”.
Holmen Iggesund – Valve Overhaul
Upon the successful completion of various projects across several different high profile sites, LEL Nuclear have expanded out into providing services to local business through our extensive list of capabilities.
LEL Nuclear have recently undertaken several projects within the Holmen Iggesund premises from steam trap surveys, condition reports to a complete valve overhaul. The valve overhaul consists of a large seized double disc gate valve which had to be jacked out with over 3 tonnes of force. Upon removal the faces were found to be damaged and therefore resulted in the requirement for lapping of the internal valve seats as well as machining both disc faces. Now with perfect sealing faces on both components, the valve was reinstalled and the discs packed accordingly to ensure a good seal was provided between the two faces.
Following re-installation, further opportunities have arisen throughout the Holmen Iggesund site where LEL Nuclear look forward to supporting them through many more complex projects.
SGMS
LEL Nuclear has played a significant role in the SGMS project situated at Sellafield. Our involvement includes the installation of all the necessary fibre and electrical components for a comprehensive overhaul of the outdated ‘Site Gate Monitoring Systems’ at both the North Gate and North Group entrances.
These systems are a vital requirement on the site, measuring for radiation/contamination of both pedestrians and vehicles upon entering and leaving the site. To meet the demands of this project, we took the initiative to expand our team by establishing a dedicated EC&I (Electrical, Control, and Instrumentation) department.
Again, by demonstrating great workmanship and attention to detail, LEL managed to secure further works on the back of this project including a decommissioning phase and a remediation phase for the sealing of ducts left by others.
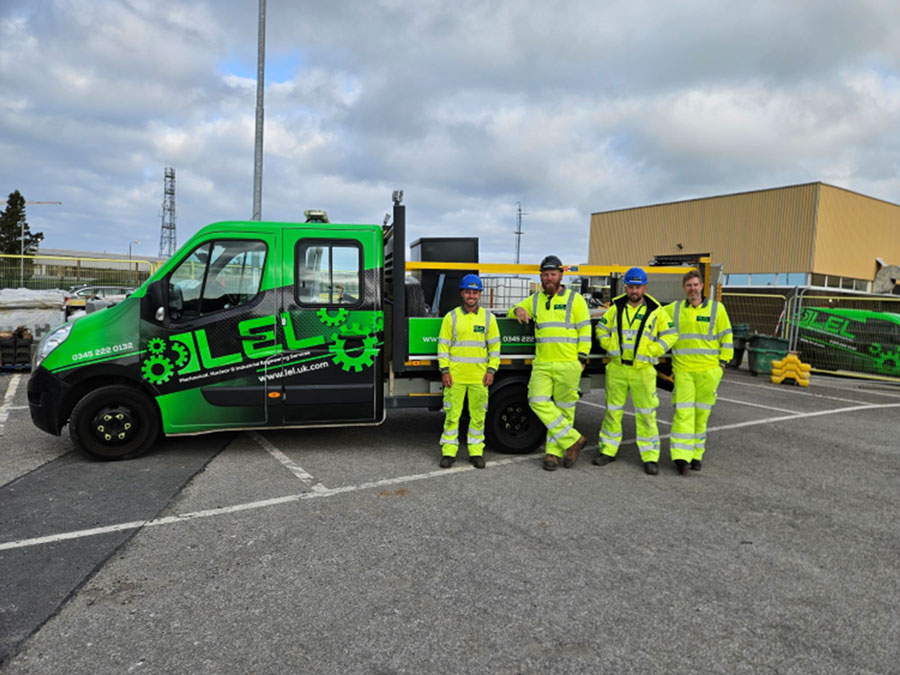